HDD: Guidance, accuracy and safety
Publicerad: 1 oktober, 2018
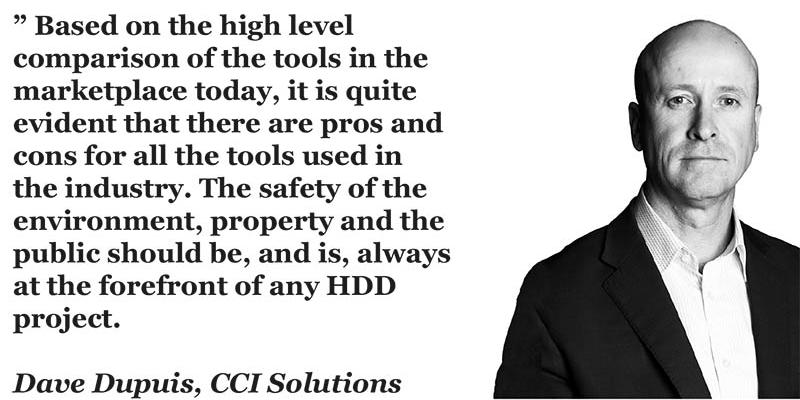
Over the last three decades of a constantly improving and evolving industry, one of the main topics of conversation consistently at the forefront of the horizontal directional drilling (HDD) sector is guidance/steering systems. Accuracy in locating subsurface drill assemblies throughout the drilling process has always been important, and is only becoming more so, with utility corridors and urban areas becoming more crowded with underground utilities.
Being able to accurately locate and guide downhole drills is not only important to ensure safe separation from existing utilities, it is also key in ensuring designed radius specifications are adhered to so that the installed product pipe is not in danger of being over-stressed and failing during installation or operation.
Many different technologies have been introduced over the years and there are multiple different systems and tools that are currently in use today. In this article, a comparative analysis of the guidance tools in the HDD industry will be presented.
The pros and cons for each system will be explored to help engineers and contractors establish what should be used for the project they are currently planning by specifying the right tool for the job. It is important to note this is a high-level comparison and further detailed investigation of the specific project is always required prior to specifying any type of equipment.
During the infancy of HDD works in the late 80s, several different techniques were used to try to get from the entry to the exit point with accuracy. During this period, accuracy meant being able to drill to the other side of the obstacle being crossed, exiting at a suitable location that allowed for the utility to be tied in and used.
The oilfield single shot survey technology that was developed in the 1930s was being used to accomplish this requirement. This proved to be quite difficult and, over several years with a significant number of failures, it was clear that a new system was required for the industry to flourish.
The introduction of Tru-Tracker technology, which significantly increased the accuracy of drills, allowed the industry to grow from a mom and pop business to the billion dollar industry it is today.
Tru-Tracker is a steering tool that uses a sensor placed directly behind the drill bit and a wire - called a coil - placed on the ground surface. The coil's position is surveyed and when pulsed with direct current it creates an electromagnetic field of known orientation.
The borehole position is determined by sensing the orientation and strength of the magnetic field at the sensor behind the drill bit. This is a tracking method that allows a verification to the calculated magnetic location and was pivotal to the advancement of the industry today.
Currently in the market, there are several types of technologies that are commonly used throughout the HDD industry. The different technologies have varying levels of accuracy and applicability to the specific constraints of the crossings. Below is a brief summary of the main types of technology used today, how they work and same of their limitations.
THE WALKOVER SYSTEM
A walkover system is typically used on small HDD rigs and small shallow crossings. This system consists of a transmitter and receiver that enables operators to locate a horizontal drilling path.
The transmitter is located just behind the drill bit and the receiver is a hand held unit . An operator holds the receiver above the ground where the drill bit is located and can follow the path of the drill from the surface.
A walkover system can monitor both the depth and direction of a horizontal drill, providing operators with real-time feedback and enabling constant adjustment of the drilling direction. Even if the terrain does not allow an operator to follow the path aboveground, the operator can move around a difficult area and pick up the location of the drill on the other side of a road or body of water.
A walkover system can monitor both the depth and direction of a horizontal drill, providing operators with real-time feedback and enabling constant adjustment of the drilling direction. Even if the terrain does not allow an operator to follow the path aboveground, the operator can move around a difficult area and pick up the location of the drill on the other side of a road or body of water.
A walkover system uses electromagnetic fields and there are limits to the depth at which they can measure; they can also be affected by interference from electrical cables. The advantages of a walkover system are that they are battery powered (negating the requirement for wireline connections within the drill pipe), necessitate little setup time and are comparatively inexpensive to own and operate.
Walkover systems fall short in situations where depth of cover and/or interference - both active and passive - are above minimal thresholds. Most electrical devices emit signals that can inhibit the ability to locate the transmitter accurately or to receive reliable roll/pitch telemetry.
Sources of active interference include traffic signal loops, buried electrical dog fences, cathodic protection, radio communications, microwave towers, cable TV, fibre-trace lines, utility data transmissions, security systems, powerlines and phone lines. Passive interference sources include metal objects such as pipes, rebar, trench plate, chain link fence, vehicles, saltwater/salt domes and ferromagnetic components of the strata, such as iron ore.
Some systems are able to overcome some active interference through the use of multifrequency transmitters. With this system, the frequency with the highest signal to noise ratio may be selected for communication with the receiver.
However, most walkover tools are not able to overcome inaccuracies that are due to passive interference sources. In addition to issues with interference, the practical depth range of walkover systems is usually significantly less than the published specifications because as the elliptical signal field emitted by the transmitter expands with depth, the closure values become increasingly subject to operator interpretation.
The walkover system also does not provide the most accurate as-builts. Since a hand-held locator is used to measure depth and horizontal heading, without a surveyor shooting the location of each survey and noting the height at which the locator was held during the survey, the as-builts furnished by this method are estimates at best.
MAGNETIC GUIDANCE TOOLS
Magnetic guidance tools are typically used for more complex, larger diameter, longer and deeper crossings. All magnetic guidance tools use magnetometers and accelerometers to calculate a directional heading.
These readings are recorded at specific intervals and the data is used to calculate the drill path's location and direction. In some areas, drills can be very accurate with the calculated data; in some locations, or more congested areas, magnetic interference can affect readings and calculations.
To compensate for this interference, an artificial magnetic field can be established along the drill path, such as using the Tru-Tracker system noted above.
This requires a wire on surface, geometrically looped in a rectangle shape, usually starting and ending at th e power source. The coil/wire is placed evenly above and twice as wide as the projected drill path is deep.
With experience and better tools, operators have learned they can place the coil/wire in a variety of manners, sometimes even completely off to one side, and maintain precise accuracy. These tools can take a long time to set up and can also be affected by interference from electrical cables.
GYRO TECHNOLOGY
A gyro is typically used on crossings with high potential for magnetic interference. It consists of a non-magnetic compass in which the direction of true north is maintained by a continuously driven gyroscope whose axis is parallel to the earth's axis of rotation.
The gyro has three axes: the spin axis, torque axis and precession axis. As the centrifugal force of the earth's rotation acts upon the gyro, the torque and precession axis will react and keep the spin axis oriented to a terrestrial meridian.
While the gyro is an extremely accurate instrument, it is relatively expensive, highly complex, dependent on an electrical power supply and subject to mechanical damage. Gyro systems can also be prone to drift over long distances, as well as “driller bias” errors that come from the accumulation of small inaccuracies from the geometric calculations that happen at each survey shot in order to estimate location.
Currently mast gyros on the market do not have a secondary measurement system in place. This means that the driller has to rely on calculated data and the location where the bit punches out of the ground as the “trothing” of the drillpath, just as they would with a magnetic steering tool without a secondary surface-coil system to confirm accurate location.
DART GYRO TECHNOLOGY
The DataTraX Azimuth while Rotating Tool (DART) combines the latest gyro technology with the industry surface magnetic tracking systems as explained above. This technology is typically used on large, long, deep and complex crossings with high potential for magnetic interference. DART technology permits drilling into magnetically compromised zones and areas not suitable for magnetic coil layout - like large waterbodies or urban areas - with accuracy and provides an indication of error build while the drilling is occurring under rotation without stopping to survey.
The drilling dynamics of this technology provides shock and vibration identification and measures potential impacts to the tools, as well as revolution s per minute, to identify drilling dysfunction issues and promote better drilling practices.
DART technology provides data acquisition that is controlled via bidirectional downlink from the surface. This allows the surface software to fund ament ally change how and when the tool acquires data to suit the drilling operation.
GUIDANCE SYSTEM ACCURACY
The importance of guidance system accuracy can be broken clown into four key areas of concern:
• Exit location - the exit of a drill at a specific surface location requires accurate guidance systems to avoid any possible environmental, property and personal injury incidents.
• Radius - the radius of curvature accuracy ensures that the product being installed does not become compromised from undue stress and/or deformation of the pipe.
• Depth - the depth or elevation accuracy ensures the product being installed is not compromised due to the external hoop stress that increases with depth.
• Centre deviation - the centreline (left/right) deviation can have a significant effect on existing right-of-way in addition to other potential safety problems when other utilities or buried obstacles are present. Inaccurate centreline data can also limit the possibility of future parallel installations.
ACCURATE AS-BUILTS AND SAFETY STANDARDS
Accurate as-builts for any future developments will allow subsequent HDD and crossings to be completed with confidence. Accurate as-built s avoid any potential safety issues and allow the owner to install new infra structure in closer proximity safely, therefore minimising the need for additional right-of-way and workspace.
CONCLUSION
Based on the high level comparison of the tools in the marketplace today, it is quite evident that there are pros and cons for all the tools used in the industry. The safety of the environment, property and the public should be, and is, always at the forefront of any HDD project.
During the planning and construction, engineers and contractors should always ask themselves if they are using the right tool for the job and did they do their due diligence to ensure they made the right decision.