Thames Tideway - navigating the challenges
Publicerad: 20 maj, 2021
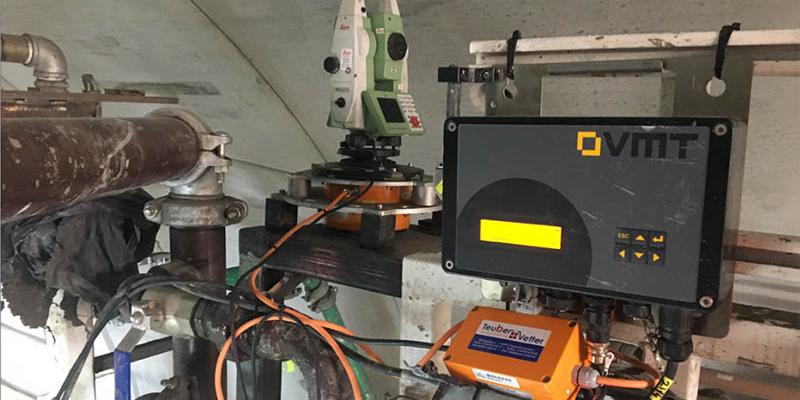
For over 160 years London, UK has been served well by the underground sewers constructed by Sir Joseph Bazalgette after The Great Stink of 1858. Although these brick-built sewers are still in good condition, over the years the growth in population to some 16 million has simply overwhelmed the system.
To alleviate this problem there is currently a new ‘Supersewer’ known as the Thames Tideway under construction, probably one of the largest utility installations currently underway in the UK.
The installation of the new sewer means that excess flows currently diverting into the River Thames will be collected and transferred to a treatment plant before cleaned effluent is discharged into the environment.
The Tideway route runs for some 25 km from Acton in the West London Borough of Ealing to the Beckton Sewage Treatment Works in the East London Borough of Newham at a diameter of 7.2 m and at depths of up to 60 m below surface.
After approval for the scheme in 2014, construction started in 2016, with tunnelling works for the new sewer commencing in 2018. The plan is to complete the tunnelling works in 2023 with all testing and commissioning works being finalised and the sewer in operation by 2025.
Thames Tideway West
Over the course of the tunnelling works, six TBMs will excavate the Tideway sewer and two smaller connecting tunnels. Tunnelling is being undertaken 24 hours per day and at the time of writing three of the six planned tunnelling sections have been completed. Once completed, tunnels are to be secondary lined to ensure water-tightness.
As part of the tunnelling works, Herrenknecht has provided one large diameter, EPB-type TBM for the construction of the Tideway Tunnel section designated Thames Tideway West C405. This section runs from Acton to Wandsworth over a length of 6,942 m using a TBM of outside diameter 8,100 mm, which allows for the installation of the secondary lining to bring the sewer to its operational diameter of 7.2 m. The contractor for this section of the project is BMB JV.
With the tunnelling being affected for use as a gravity sewer, the line and level of the route are vital to the success of the installation over the whole project.
Tunneling support systems
For this particular section, specialist guidance system designer and manufacturer VMT (based in Bruchsal, Germany) provided several tunnelling support systems to guide and aid the TBM through its challenging route.
For the tunnel guidance operation, VMT provided:
- TUnIS Navigation TBMLaser – the initial primary navigation system which can be used for EPB, mixed shields and hard rock TBMs. The system is based on the use of a total station and a target unit installed within the TBM shield, which determine the current advance position of the TBM. When using segment machines using a small or limited laser window, the TBM position is continuously calculated during short-term interruptions. TUnIS Navigation TBMLaser offers high reliability as it provides temporary navigation through the thrust cylinders of the TBM.
- TUnIS.moving station – a new assistance system that enhances a laser and target-based navigation system in large diameter tunnelling. With TUnIS.moving station the total station is not mounted on the tunnel wall, but travels on the gantry of the TBM.
- TUnIS Office – a system that provides real-time navigation and ring data from one or more TBMs. The navigation system may be directly monitored from the site office. The user may immediately analyse and document current and historical data, and all persons involved in the project may track the tunnelling process: on the machine, in the site office, through web server, or on mobile terminals. Several users may simultaneously access the entire functionality of the navigation system in real-time without affecting the construction process.
- VDMS.Process – a web-based process data management system developed by VMT to handle complex infrastructural building projects. The system processes and correlates data from a variety of different sources, analyses them and displays them in user-friendly form so that they can be made available to project managers worldwide in a wide range of output forms. VDMS ensures full information transparency and supports the efficient control of both the TBM and many other operating processes within the tunnelling project.
Tunnelling works on this section started on 26 April 2019, with breakthrough on 24 September 2020. The customer was satisfied with the breakthrough accuracy.
Moving station
Supporting and simplifying the surveyor and TBM engineers’ day-to-day activities was the latest development from VMT’s navigation range, the TUnIS.moving station. The TUnIS.moving station determines and calculates all data and information that is necessary for navigating the TBM along a tunnel axis. The high information content of the data displayed ensures optimum control of the machine position, thus helping to maintain a uniform shield run with minimal deviations from the desired route. The position and tendencies are continuously displayed to the shield operator, allowing vertical or horizontal curves to be easily and precisely controlled.
Three prisms installed on the tunnel wall with an active electronic laser target in the shield of the TBM are used for exact determination of position. In the first step, the exact current position of the total station is determined using the prisms. In the second step, the current position of the laser target is determined - and thus, the position of the TBM.
This new system undertook its earliest and very effective trials on the London Tideway Tunnel, in parallel with the initial primary navigation system (which was also provided by VMT). The trials were so successful that the tunnelling operation was moved onto the new TUnIS.moving station system, replacing the primary VMT standard navigation system for 560 metres of the advance.
Hardware central box
Also tested on the site was the new SLuM.Connect hardware central box, as part of the existing automatic tailskin clearance measurement system, SLuM Ultra. The ring build is a decisive part of mechanised tunnelling with segmental lining. To determine the optimal installation of the ring it is necessary to observe the current position and orientation of the TBM, plus the position of the last built ring. SLuM Ultra enhances the ring build process by measuring the reference ring position relative to tail-skin axis with millimetre- accuracy. The TUnIS.App was also widely used by site engineers and surveyors, allowing remote operation of the navigation system from outside the control cabin.
Roy Behrend, Chief Surveyor Tunnel for the BMB-Joint Venture on the project said: “Communication was really good with VMT and their site engineers for the testing and implementation of the new TUnIS.moving station system. There was always immediate ongoing support for VMT’s navigation systems and TUnIS software. Support was also available remotely. The TUnIS software package is well developed and its menu systems allow for ease of use.
The system is very well supported by VMT. VMT Support Engineers also have remote access to the system which allows for easy system maintenance and testing. I would not hesitate to recommend or use VMT products again."